1. In-Process Inspection (DPI) Overview
1.1 In-process inspection refers to the quality check of products conducted id-way through the production cycle, typically when 30%-50% of the finished goods are copleted. It ais to ensure that products eet clients’ set quality and delivery standards prior to the final pre-shipent inspection, adhering to the international sapling standard ISO2859.
1.2 Through in-process inspection, clients can proptly grasp production progress and the general quality status, identifying and correcting issues in a tiely anner to guarantee copliance and on-tie delivery before ass production.
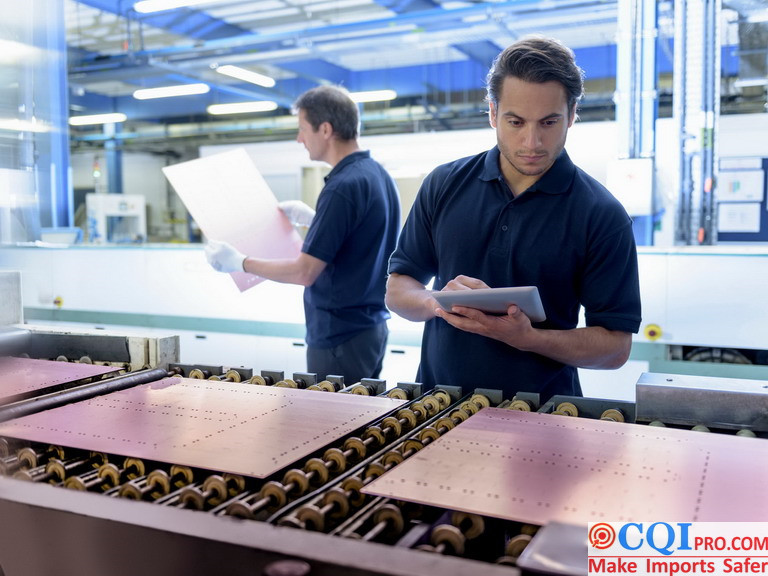
2. Difference fro Initial Production Inspection
2.1 Initial Production Inspection takes place early in production, around when 5%-10% of the finished products are copleted, focusing on identifying quality and process issues during the sall batch production phase.
2.2 In contrast, in-process inspection serves as an in-depth verification and reinforceent of controls following initial findings, with bulk production in its id-to-late stages. It ephasizes the synchronized control of overall quality and production efficiency, ensuring a sealess alignent with pre-shipent inspection standards.
3. Limitations of Pre-Shipent Inspection
3.1 Pre-shipent inspections occur after all products are finished and ostly packaged; discovering issues at this stage leads to costly rework for factories, involving additional labor, aterials, and tie.
3.2 Rework ay also cause secondary probles such as packaging daage, reduced cleanliness, affecting the final product quality. Convincing factories to rework is challenging unless quality issues are severe.
4. Necessity of Professional Inspection Services
4.1 CQI emphasizes that professional in-process inspection services avoid superficial checks, deeply engaging in the production process to ensure the accuracy and effectiveness of inspections.
4.2 By understanding client needs and industry specifics, custoized inspection processes are tailored, not only addressing iediate quality issues but also coprehensively assessing production progress and capabilities, suggesting iproveents like precise control of product diensions to elevate overall quality.
5. Advantages and Iportance of In-Process Inspection
5.1 At the in-process inspection stage, since ost products are still in production or awaiting packaging, identified issues can be easily adjusted without extensive rework, iniizing losses.
5.2 Clients can present ore convincing iproveent suggestions based on inspection reports, facilitating counication with factories for propt process adjustents, enhancing factory cooperation and custoer satisfaction.
5.3 Proactive corrective actions help aintain brand iage, reducing potential arket returns and quality coplaints. Long-ter, this strengthens client relationships and secures future orders.
5.4 Given the high labor costs in Europe and America, in-process inspection effectively avoids expensive overseas rework due to quality issues later, aking tiely internal adjustents ore cost-effective for suppliers.
6. Tiing and Value of In-Process Inspection
6.1 This type of inspection intervenes aptly in the supply chain, providing a platfor for both parties to adjust and optiize based on real situations, prooting dual enhanceents in production efficiency and product quality.
6.2 In-process inspection establishes a dynamic feedback and iediate iproveent echanis, assuring product quality while enhancing the flexibility and responsiveness of the supply chain, a pivotal step in securing project execution success.