– 1.1 A Vital Link in Supply Chain Management
In the intricate landscape of international trade, supplier quality audits form a cornerstone of ensuring a healthy supply chain operation, complementing routine inspection services to establish a foundation for risk management. It transcends product inspections, focusing instead on preemptively identifying and assessing suppliers’ capabilities and reliability.
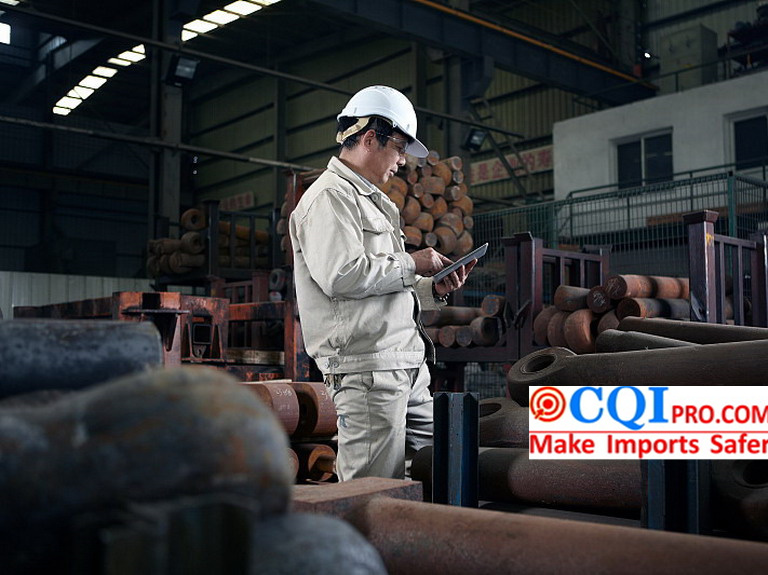
– 1.2 The Synergistic Role of Audits and Inspections
While quality inspections concentrate on product-level quality control, aiming to instantly detect and rectify issues, audits delve into factories beforehand, systematically scrutinizing production systems, management competence, and environmental compliance, thereby solidifying the groundwork for subsequent collaborations.
– 1.3 The Significance of Pre-Engagement Audits
Conducting factory audits prior to formal orders significantly bolsters the verification of suppliers’ credentials and capabilities, mitigating major risks that could impact product quality and delivery timelines, and constitutes the primary step in fostering trust and cooperation with suppliers.
Selecting and Implementing Supplier Quality Audits
– 2.1 Audit Standards and Procedures
Most audits adhere to international standards such as ISO 9001 and ISO 14000, comprehensively covering management system evaluations, a process that typically spans at least two days. Despite similarities in service process across inspection firms, the specifics and focal points vary.
– 2.2 Challenges in Selecting Audit Services
The market challenge lies in numerous inspection companies promoting complex and costly audit schemes tailored more towards the stringent requirements of large retailers and international brands, which prove impractical for cost-conscious small and medium importers.
Optimizing Audit Services to Meet Market Demands
– 3.1 Responding to SME Needs
QAONE company addresses the specific needs of small and medium importers by offering optimized, cost-effective, and targeted supply chain quality audit services, enabling these enterprises to more agilely identify and verify suppliers in the global market, highlighting the advantage of cost-performance.
– 3.2 Limitations of Large Inspection Firms
In contrast, large inspection companies, bound by their scale and operational models, incur higher service costs and exhibit lower flexibility, primarily catering to premium market clients. This creates a market niche for inspection service providers focused on serving SMEs.
Future Trends: Differentiation and Social Responsibility Audits
– 4.1 Changes in Supply Chains in the Internet Era
With the digitization of consumer markets, small and medium importers increasingly rely on online platforms for business expansion, necessitating inspection services that are more adaptable, efficient, and responsive to rapidly evolving market demands.
– 4.2 The Importance of Social Responsibility Audits
As an advanced aspect of supply chain management, social responsibility audits not only focus on production efficiency and quality but also supervise factories’ social responsibility performance, encompassing employee welfare and working conditions. Factories passing such audits often excel in comprehensive management, producing higher quality products, attracting consumers and businesses committed to sustainability.
In conclusion, supplier quality audits, an indispensable component in international trade, are trending towards addressing the needs of SMEs and emphasizing social responsibility and sustainability, ushering in a new era in global supply chain management.